Dieses Seminar/Webinar kann nicht gebucht werden. Alternative Termine für dieses Seminar/Webinar und ähnliche Veranstaltungen finden Sie in der Übersicht nach Thema..
Für viele Seminare und Webinare gibt es auch Aufzeichnungen, die Sie jederzeit bestellen und anschauen können. Diese Aufzeichnungen finden Sie in einer themensortierten Liste.
Oder senden Sie uns Ihre Anfrage einfach über das folgende Kontaktformular.
* auch unkompliziert per Kreditkarte bezahlbar
Weitere Termine vor Ort
Weitere Termine vor Ort nicht verfügbar
Weitere Termine online
Weitere Termine online nicht verfügbar
Aufzeichnung nicht verfügbar
This course is part of the GMP Certification Programme "ECA Certified Technical Operations Manager"
Haben Sie noch Fragen?
Wir stehen Ihnen für weitere Auskünfte gerne zur Verfügung.
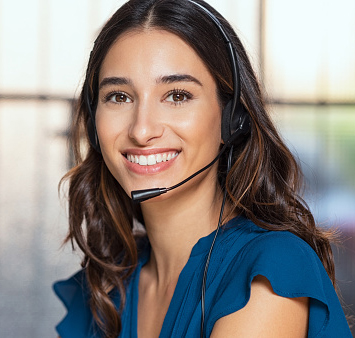
E-Mail: info@concept-heidelberg.de
Teilnehmerstimmen - das sagen andere über unsere Seminare: